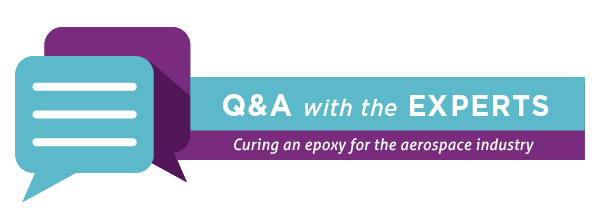
Join Robert Michaels, Vice President Technical Sales as he answers questions about how to properly cure an epoxy for the aerospace industry.
Q: Can you please tell us about curing options for an epoxy in the aerospace industry and regarding that, what the pertinent properties involved are, especially as it relates to the addition of heat for curing?
A: There are many ways to categorize epoxies and one way would be to group those that cure at room temperature and those that require heat for curing. Most two part systems are formulated to cure at room temperature and simply require the mixing of Part A (the resin) and Part B (the curing agent). There are a number of special two component systems as well as one part systems (where no mixing is required) that require heating at 250-350°F, usually in an oven. Since the second group requires additional processing, the operative word that comes into focus is trade-off. With the first group, that is the room temperature curing materials, not having to add heat is a far easier way of doing things. However, adding heat to the epoxy systems that normally cure at room temperature, will accelerate the rate of cure and boost the performance profile. Regarding the two part epoxies and one part systems that require heating, the trade-off for having to add heat is achieving superior performance attributes, such as temperature resistance, electrical properties, etc.
More importantly, a fundamental concept that we're trying to express is, that when you get down to the “nitty gritty”, epoxies do not fully cure at room temperature. This can be unnerving; most people think room temperature curing epoxies fully cure after X number of days and many companies put this in their literature, but in reality, they don't. Epoxies only fully cure and optimum properties are only totally achieved when heat is added. The amount of heat and the duration of it, depends upon the system. Even with the most basic type system, such as the five minute system perform better if heat is added as a “post cure”. This whole idea of adding heat is not widely understood or appreciated, but it a vital element in using epoxies.
Q: Are there specific applications where adding heat during or after cure is advantageous?
A: In nearly every application the answer would be yes, particularly in aerospace, where the requirements are so rigorous and the qualification process is so demanding. One can easily choose a two part room temperature curing product, but it's crucial for the engineer to know that adding heat will result in a better system. There is a plethora of data and documentation that has been provided over the years by some of the major companies involved in the manufacturing of epoxy resins and curing agents on this point.
It is only fair to note that in many applications, optimum properties that are achieved by added heat may not actually be needed. For example, there are a number of non-critical aerospace applications, where straightforward room temperature curing achieves the desired result. However, in most aerospace situations the rigorous testing and qualification procedure almost demands post curing with heat to optimize properties, with a side benefit of accelerating the cure as well.
Unfortunately if the issue of adding heat and post curing is discussed, one often encounters a moan and a groan. When the suggestion is made that adding heat is strongly recommended, there are many excuses offered, such as a lack of availability of an oven, it’s going to take too much time, etc. But, the bottom line is heat is needed to get the desired results. A good example of a situation where heat must be added to achieve a desired goal is with low outgassing. Simply put, it is absolutely mandatory to add heat to complete the cross-linking in the epoxy reaction so that the standard (low outgassing) is achieved. That is just the nature of these materials.
Q: Are there other values that would benefit from adding heat during the curing process?
A: Yes, for sure; take, for example, temperature resistance. One of the common ways of measuring temperature resistance is with glass transition temperature (Tg). For example, let’s say with straight room temperature curing system, there is a hypothetical glass transition temperature of 100°C. If heat is added for one hour at 150°C, Tg will go up maybe 10-15°C. Adding heat for another 4 hours at 150°C will further increase the Tg by another 5-8°C, and in some cases, adding heat for 12-24 hours will actually further extend the Tg by 2-3°C. With two part epoxies and one part systems that require heat for curing, post curing for many hours (12-24+) at temperature above the Tg (50-100°C) can increase the glass transition temperature by 25-30%.
Q: Would you then recommend that room temperature curing epoxies be oven cured for 24 hours?
A: It is certainly not necessary to add heat for 24 hours—that’s an awful lot of heat and the time period is simply not realistic. The point of mentioning the 24 hour period in the previous paragraph is to show conceptually how many systems require extraordinarily long heat cycles to obtain the elusive goal of optimum properties. Realistically, adding heat for a few hours is usually sufficient.
Q: What is the curing process for submitting an epoxy for low outgassing testing?
A: For a two part room temperature curing epoxy, if we were going to submit that material for low outgassing testing, we would cure it at room temperature overnight and then add heat, 100-150°C for 2-3 hours at the very least, and that will get us where we want to go. On our data sheets, we are very careful and explicit to note that the optimum cure for these room temperature systems is to let them set up at room temperature “overnight”, so that the epoxy doesn't run. After it has set up, it is desirable and beneficial to add heat. One very important issue related to adding heat is that when an epoxy is still liquidy adding heat will lower the viscosity quickly and dramatically. This can cause undesirable flow of the material. However, if the room temperature curing system is allowed to gel first, and then the heat is added, the goal of achieving additional cross-linking without unwanted “running” of the material is eminently doable.
With two part epoxies that require heat curing and the one part epoxies, the normal curing schedule is followed and then a post cure of at least few hours at 100-150°C is added to the curing schedule to optimize the properties for this kind of test. These epoxies will flow during the curing cycle. The only way to avoid this is with a specially formulated paste type epoxy that is designed not to flow with of addition of heat.
Q: Are there any other noteworthy examples of the benefits of adding heat, perhaps in another industry?
A: Absolutely, achieving biocompatibility for medical device applications is a prime example of this. In a word, no formulations company would submit an epoxy system for biocompatibility testing without post curing with heat, it is that critical!
Q: Are there other property tests in the aerospace industry where post curing is advantageous?
A: I touched upon low outgassing earlier, but there are certainly other properties as well. Take, for example, electrical insulation testing. The main test data for aerospace or electrical engineers in these applications is typically the dielectric constant, dielectric strength, dissipation factor and volume resistivity. All of these are affected positively by post curing or adding additional heat. Again, a good rule of thumb is to add 50-100°C above the Tg, for at least a few hours.
Q: Is this principle the same for electrical conductivity?
A: Yes it is. With electrical conductivity, if you have a two part system (room temperature curing) and you let it cure for 2-5 days, it will be very conductive. However, if you add additional heat, the cross-linking is more intense and the conductivity is higher. How much heat? It depends upon the Tg and how many hours you add it. It doesn't have to be 24 hours as in the extreme scenario mentioned earlier. A few hours of additional heating is more than adequate for most applications.
Q: Besides electrical and thermal properties, what else can benefit from the addition of heat?
A: No question about it; with chemical resistance, it makes all the difference in the world. These materials simply won't resist chemicals nearly as well without adding heat. I can't think of a single application in aerospace or otherwise that adding heat doesn't help with chemical resistance.
You can extend that to include physical strength properties, such as modulus, tensile strength and compressive strength as well.
In fact, even in special applications where thermal conductivity and electrical insulation is required, adding heat enhances the thermal conduction and electrical insulation properties of the system.
This is a very brief overview of the importance of adding heat to epoxy systems. This is often not emphasized nearly enough primarily because it is not a good selling point. We focused on epoxies here, as they are the go-to polymeric type material for bonding, sealing, coating and encapsulation applications that occur in the aerospace industry.
Master Bond offers a wide range of epoxies that meet the rigorous application requirements of the aerospace industry.
Meet Our Tech Expert: Robert Michaels
Robert Michaels has been lead coordinator for all technical activities at Master Bond for the past 25 years. Supervisor of technical support activities to both end users and as it pertains to quality control, Robert is also involved in product development and regulatory issues. He has played an integral role in implementing growth and expanding the customer base both domestically and internationally to various high-tech industries including electronics, aerospace, medical device manufacturing, opto-electronics, OEM and related industries.