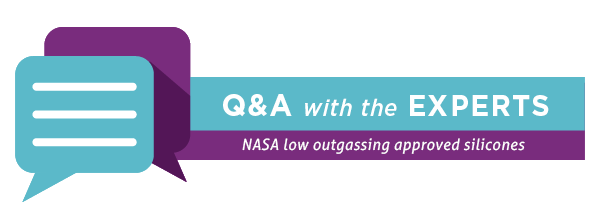
Join Venkat Nandivada, Manager of Technical Support at Master Bond, as he answers questions about NASA low outgassing approved silicones.
Q: What are some of the main considerations when formulating adhesive products for the aerospace industry?
A: The biggest consideration for most aerospace applications is the NASA low outgassing specification. ASTM E595 is the industry standard test for measuring outgassing in adhesives and other materials. Developed by NASA to screen low outgassing materials for use in space, the test determines the volatile content of material samples placed in a heated vacuum chamber. You can learn more about the test details here.
Q: Are there any new products that Master Bond has released for the aerospace industry?
A: Master Bond has just introduced a line of one and two component silicones that meet NASA low outgassing requirements. MasterSil 920-LO, MasterSil 921-LO and MasterSil 922-LO are one part silicone systems that cure at room temperature based on the humidity in the air; where the higher it is, the faster the cure. Our two part silicones include MasterSil 970-LO, MasterSil 971-LO, MasterSil 151TC and MasterSil 151S, which are addition cured systems, meaning that they do not require air for complete crosslinking.
Q: What makes these silicones such desirable products?
A: In addition to passing NASA low outgassing testing, these systems all offer impressive flexibility, thermal cycling capabilities, and high temperature resistance up to 400°F or 500°F depending upon the system. These silicones also offer very low stress, making them well suited for use with sensitive electronic parts.
Select systems such as MasterSil 151TC and MasterSil 151S feature a thermal conductivity of 4-6 and 9-11 BTU•in/ft²•hr•°F [0.58-0.83 and 1.30-1.59 W/(m•K)], respectively. MasterSil 151S is a silver filled, electrically conductive system that offers very low volume resistivity at room temperature.
This family of silicones is easy to handle, and many systems offer good flow properties. Some offer a higher viscosity, such as the MasterSil 922-LO, which has a non-drip paste consistency.
In optical applications where a clear silicone is required, MS920-LO, MS921-LO, and MasterSil 971-LO could be considered, due to their optical clarity and excellent light transmission properties.
Q: Can these systems fill the need for highly specialized applications?
A: As a matter of fact, MasterSil 920-LO is ideal for conformal coating and encapsulation applications. Conformal coatings enhance the reliability and long-term performance of electronic assemblies by providing superior protection against moisture, dust, dirt, abrasion, and other contaminants.
Another example is MasterSil 151S, which can be used as a form-in-place, electrically conductive gasket material. It enables precise application and it can cure in wide and deep cross sections.
Q: Other than aerospace, where can this line of products be used?
A: The aforementioned properties make these silicones well suited for many applications across the electronics, optical, fiber-optics and OEM industries.
Meet Our Tech Expert:
Venkat Nandivada has been a Manager of Technical Sales at Master Bond since 2010. He has a Masters in Chemical Engineering from Carnegie Mellon University. He analyzes application oriented issues and provides product solutions for companies in the aerospace, electronics, medical, optical, OEM and oil/chemical industries
Top Performing NASA Low Outgassing Rated Silicone Systems
![]() |
MasterSil 151S Addition curing, two part silicone for use as an adhesive, sealant, coating or form-in-place gasketing material. Despite its silicone chemistry, it passes NASA low outgassing specifications. It is ideal for applications where low stress is required. |
![]() |
MasterSil 151TC Optically clear, addition curing potting, encapsulation, sealing compound. Low shrinkage upon cure. Resists up to +400°F [+204°C]. Shore A hardness 50-60. Highly resistant to water. Long pot life. Primarily in thermal management applications. |
![]() |
MasterSil 920-LO RTV silicone for sealing, coating and small encapsulation. NASA low outgassing approved. Superb optical clarity. Good flow properties. Non-corrosive. Soft durometer facilitates usage with sensitive components. Excellent electrical insulator. Withstands thermal cycling. |
![]() |
MasterSil 921-LO Passes NASA low outgassing test requirements. Spreads evenly and smoothly. Bonds well to many substrates. Wide service temperature range of -175°F to +500°F. Neutral curing, non-corrosive type system. |
![]() |
MasterSil 971-LO Meets ASTM E595 specifications for low outgassing. Optically clear, two part system with one to one mix ratio by weight. Serviceable from -120°F to +400°F. First class electrical insulator. |
![]() |
MasterSil 970-LO Moderate viscosity, two component silicone adhesive, sealant, encapsulant. Passes NASA low outgassing test requirements. Vacuum compatible. Withstands rigorous thermal cycling and shock. White color. Good flow properties. Serviceable from -120°F to +400°F. |