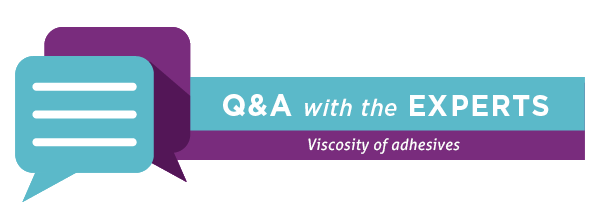
Join Venkat Nandivada, Manager of Technical Support at Master Bond, as he answers questions about how to select an adhesive based on its viscosity.
Q: What is viscosity?
A: Viscosity is a fluid’s resistance to gradual deformation by shear and/or tensile stresses.
Q: How is viscosity of an adhesive measured?
A: Viscosity is typically measured at 75°F in cps. Master Bond formulations come in a wide range of viscosities from as low as 200 cps to in excess of 1,500,000 cps.
Q: How would you select an adhesive based on viscosity for an application that involves filling small components?
A: Based on the geometry of the gaps, along with the volume occupied by the components, a product with a low viscosity offering good flow characteristics, might be useful. The specific range of the viscosity might depend on the necessity for wicking inside some of the smaller components within. In certain situations, for example impregnation, an extremely low viscosity compound would be the ideal choice. The addition of heat as well as vacuum impregnation techniques can be used to help facilitate flow properties even further.
Q: If we look at an application where the adhesive needs to stay in place, yet be dispensible, what viscosity would you recommend?
A: In this situation, the thixotropic nature of the product---i.e. thick while it is static and flowing when it is agitated—could play a key role. An example of this type of application would be a glob top encapsulant. A compound which can be dispensed, yet stay in place after it is applied, would be critical.
Q: What is the right viscosity for an adhesive to bond vertical surfaces?
A: A compound which does not flow during application, essentially a non-drip compound, would be the best choice. Note that there are certain products which could remain non-drip even during the curing process at elevated temperatures.
Q: How can the viscosity of an adhesive be adjusted in an existing design, assuming the materials cannot be changed?
A: Since viscosity is generally a function of the temperature at which the product is applied, if you were to pre-heat the substrates or the compound itself, this process would influence the viscosity. One of the potential trade-offs might be a reduction on the working life of the product.
Another way to influence the viscosity could be to use a thinning agent or reactive diluent, depending on the type of adhesive used. The trade-off here could involve a loss of some of desirable cured properties.
Q: How can the viscosity of the product be increased in order to lessen the flow?
A: In certain cases, inert fillers can be added to increase the viscosity. One commonly used thickening agent is fumed silica, which helps to increase the viscosity significantly. Additionally, some thermally conductive fillers help not only to increase the viscosity, but also to dissipate heat.
Master Bond compounds are available in a wide range of viscosities to meet specific application requirements.
Meet Our Tech Expert: Venkat Nandivada
Venkat Nandivada has been the Manager of Technical Support at Master Bond since 2010. He has a Masters in Chemical Engineering from Carnegie Mellon University. He analyzes application oriented issues and provides product solutions for companies in the aerospace, electronics, medical, optical, OEM and oil/chemical industries.