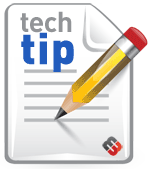
Some epoxy compounds successfully meet thermal stability testing standard ASTM D3850-12 per MIL-STD-883J Section 3.5.2 & 3.8.5 for military applications, however these systems can also be used across many other industries where thermal stability is an important requirement. The thermal stability test is not just an aggressive check for the high temperature serviceability of such compounds, but it also is an excellent starting point for using such compounds in high temperature applications. Other considerations to keep in mind are the continuous, as well as the maximum service temperature range, thermal cycle ramp speeds, and other thermally induced stresses in the application. Some common non-military applications that benefit from compounds that pass MIL-STD-883J include downhole oil equipment, lasers, satellite systems, electronics, power tools, as well as various automotive applications.
MIL-STD-883J testing for polymers involves thermal stability analysis, by running a Thermogravimetric Analysis (TGA). The thermal stability is determined by heating the specimens from room temperature to 200°C at a heating rate of 10°C/minute in a nitrogen atmosphere. The thermal stability of the cured material is determined by the weight loss at 200°C. For the polymer compound to pass the test, the weight loss must be less than or equal to 1.0 percent of the cured material weight prior to the exposure to the temperatures.
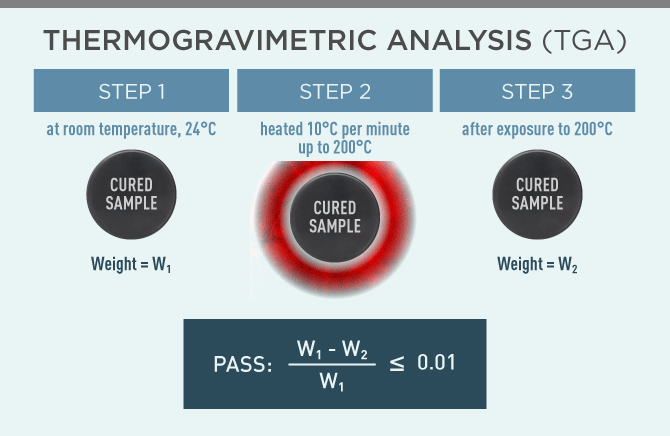
These thermally stable adhesive systems offer many other advantages especially over traditional fastening techniques, such as improved load bearing capacity, stress distribution, resistance to cyclical fatigues, protection against chemicals, and light weighting, to name a few. Designers and engineers must be mindful of the processing considerations such as surface preparation, and cure schedules while selecting the right product. It is best to consult with the supplier’s recommendations while choosing the adhesive, sealant, coating, or potting compound, and also for the best processes to use.
To read more about Master Bond adhesives that passed MIL-STD-883J testing please click here.
MIL-STD-883J Certified Adhesive Systems
![]() |
EP17HTDA-1 Single component heat curable epoxy adhesive/sealant. Non-drip system. Resists up to 525°F. Meets NASA low outgassing specifications. Meets MIL-STD-883J Section 3.5.2 for thermal stability. High lap shear, tensile and compressive strength. Tg of 230-240°C after post cure. |
![]() |
EP21TDCHT High strength, high temperature resistant, two part system with excellent bond strength and thermal cycling capabilities. Serviceable from -100°F to +350°F. Meets MIL-STD-883J Section 3.5.2 for thermal stability. Moderate viscosity. Superior toughness. Withstands vibration, impact, shock. Good dimensional stability. Convenient one to one mix ratio. Dependable electrical insulation properties. |
![]() |
EP33 Meets MIL-STD-883J Section 3.5.2 for thermal stability. Room temperature curing system. One one mix ratio by volume. Superb chemical resistance and dimensional stability. Shore D hardness 85-90. Suitable for bonding, sealing, coating. Withstands 1,000 hours 85°C/85% RH. Serviceable from -60°F to +450°F. Easily machinable. |
![]() |
EP46HT-1AO Thermally conductive/electrically insulative heat resistant epoxy compound. Requires oven curing. Meets NASA low outgassing specifications. Meets MIL-STD-883J Section 3.5.2 for thermal stability. Excellent dimensional stability. Withstands 1,000 hours 85°C/85% RH. Serviceable from -100°F to +550°F. Tg 215-220°C. |
![]() |
Supreme 11AOHT Thermally conductive, electrically insulative epoxy adhesive. Meets MIL-STD-883J Section 3.5.2 for thermal stability. High peel and shear strength properties. Non-drip system. Resists -112°F to +400°F. Toughened system. Can withstand rigorous thermal cycling. Convenient one to one mix ratio by weight or volume. Cures at room temperature. |
![]() |
Supreme 12AOHT-LO One component, heat cure system for bonding, sealing. High strength product. Service operating temperature range from 4K to +500°F (260°C). Resists aggressive thermal cycling and shock. Substantial thermal conductivity of 9-10 BTU in/ft2 hr °F. Smooth thixotropic paste. NASA low outgassing approved. Meets MIL-STD-883J Section 3.5.2 for thermal stability. Withstands 1,000 hours 85°C/85% RH. |