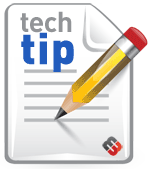
Use of different filler types, shapes, sizes, densities, concentrations play an essential role in controlling the flow of liquid epoxy adhesive formulations. Powders, flakes, spheres, granules, fibers, can be added/properly dispersed to obtain the desired rheological characteristics required by the end user. High, medium, low viscosity systems have been incorporating fillers such as aluminum, alumina, graphite, silica, silicon carbide, zinc in appropriate load volumes. Mixing, pumping, application by brush, spray, syringe, cartridge will be facilitated by their excellent rheological properties. Additionally these products offer consistent, reproducible bond line thicknesses without air entrapment to maximize bond strength and structural integrity of the mated joints.
It is important to note that viscosity/flow of epoxy adhesives will be affected by temperature and stirring/agitating. Viscosity of most grades will decrease with an increase in temperatures. Select compounds can be cured at elevated temperature without decreasing viscosity. This prevents the adhesives from flowing out before and during the curing process. Often it is necessary to adjust/modify filler content to achieve the most advantageous balance between performance and flow properties. It is important to note that adding fillers can affect abrasion/chemical resistance, heating, aging, strength, shrinkage, exotherm of epoxy systems.
Thixotropic paste adhesive systems can be precisely dispensed for controlled bond line thickness. They are blended to flow more readily/become less viscous under a constant shear rate. When the shear rate falls off the viscosity will rise to a more viscous state and the adhesive will regain its original higher viscosity. The more the system is shaken, the lower its thickness. Recovery time to its original viscosity is time dependent. Some of these products will not sag/creep, can be applied on vertical surfaces without slumping and can be employed as gap fillers for cavities, cracks, holes.